Déterminer le risque machine est un facteur clé de la réussite d’une démarche de prévention des conditions de sécurité. Une mauvaise conception des moyens de protection ou des circuits de commande des machines peuvent être à l’origine de dysfonctionnements. Avec quelquefois des conséquences graves pour la sécurité des opérateurs ou des personnes qui interviennent à proximité.
Une machine industrielle est par défaut dangereuse à cause de nombreuses parties en mouvements, coupantes, laser… Il est donc impératif d’étudier les risques et dangers liés à son utilisation normale.
Afin d’utiliser votre machine dans les meilleures conditions de sécurité et d’éliminer les risques avant qu’ils arrivent. Il est nécessaire de faire une étude de sécurité, tout en se basant sur les normes industrielles liées à la machine et à son fonctionnement. Et cela de manière à réduire les risques pendant tout son cycle de vie.
Pour cela nous allons définir et déterminer les risques qui se rapportent à votre machine. Les normes CEI/EN 62061 et CEI 61508 vont nous servir dans la démarche.
Limites d’utilisation et de fonctionnement
Pour connaitre les risques liés à une machine il faut avant tout savoir où elle sera installée. Il faut vérifier dans quel environnement ; en extérieur, en intérieur ; qui à accès à l’installation…
Il faut toujours prendre en compte les facteurs techniques et humains lors de la conception et l’installation d’une machine. Le but est de réduire et de prévenir aux mieux les accidents pouvant survenir.
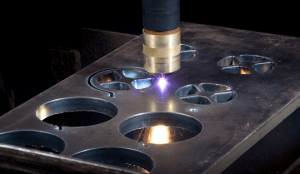
Pour illustrer la démarche nous allons prendre comme exemple une table de découpe plasma CNC. Cette machine servant à couper des métaux doux en utilisant un arc électrique d’une température d’environ 18 000 °C. Au point de contact sur la pièce métallique, cela provoque une fusion quasi instantanée du métal.
Cette machine lors de la découpe génère beaucoup d’étincelles. lLensemble du portique où est fixée la torche de découpe se déplace sur rails créant un risque d’écrasement.
Identification des phénomènes dangereux
Pour connaitre le niveau de risque nous utilisons les tableaux des normes de sécurité machine CEI/EN 62061, CEI 61508 et ISO 12100 : 2010.
Démarche à suivre :
- Etape 1 : détermination des limites de la machine
- Etape 2 : Identification des phénomènes dangereux
- Etape 3 : Estimation du risque
- Etape 4 : Evaluation du risque
- Etape 5 : La machine est-elle sûre ?
Non Réduction des risques : – mesures de conception -fonctions complémentaires -information du personnel |
Oui
Fin de l’étude |
Dans notre exemple les risques possibles sont :
- pincement / écrasement
- brûlures légères
- brûlures graves
Notre machine ayant un chariot mobile se déplaçant sur une crémaillère cela peut entrainer le sectionnement d’un doigt. De plus le métal en fusion génère des étincelles pouvant causer des brûlures plus ou moins graves en fonction de la zone du corps touché. Pour connaitre le niveau de sécurité nécessaire à appliquer il faut faire une évaluation des risques.
Evaluation des risques calcul du SIL
- SIL : Safety Integrity Level – niveau de sécurité intégré
- PL : Performance Level – niveau de performance
Il s’agit des deux noms que l’on peut rencontrer lorsque l’on nous parlons de sécurité machine SIL étant la plus répandue nous utiliserons cette appellation.
Le niveau SIL prend en compte la gravité de l’accident, sa fréquence d’exposition dangereuse (à partir de quelle durée d’utilisation de la machine le risque apparaît), la probabilité d’apparition et la possibilité de limiter ou d’éviter l’accident.
Sous forme de tableau nous allons voir comment définir le niveau de sécurité à appliquer à la zone créant le danger. Pour cela il faut connaitre la gravité du danger :

Dans notre exemple la gravité est de niveau 3 car on a la perte d’un doigt. Il faut retenir le 3 il nous servira pour le tableau final.
Une fois la gravité obtenue on regarde la fréquence d’exposition dangereuse, à partir de quelle durée d’utilisation de la machine le risque peut se rencontrer.
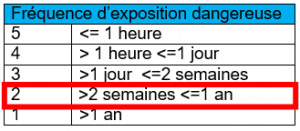
Il s’agit d’un accident qui peut arriver plusieurs fois par an, mais il est rare que cela se produise donc, la fréquence choisie est >2 semaines et <=1 an, la fréquence est donc égale à 2.
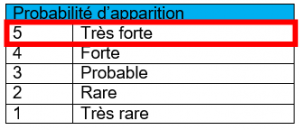
A tout moment l’accident peut arriver sans être dans un stade précis d’utilisation, donc sa probabilité d’apparition est très forte, son niveau est égal à 5.
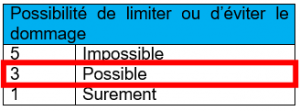
Il est possible de protéger la zone du rail mais il est impossible d’empêcher tout risque d’accident sans ajouter une sécurité matérielle (carte de protection, détection d’obstacle…)
Une fois que l’ensemble des tableaux étudié pour notre accident nous regroupons les résultats.
- Gravité : 3
- Fréquence d’exposition dangereuse : 2
- Probabilité d’apparition : 5
- Possibilité de limiter ou d’éviter le dommage : 3
Le résultat du tableau de gravité va nous servir à connaitre la dangerosité de la zone de la machine et l’addition des résultats des 3 autres tableaux, la classe de sécurité à appliquer.
Nous obtenons :
2 points de fréquence + 5 points de probabilité + 3 points de possibilité d’éviter un danger.
Nous avons donc une gravité de niveau 3 et une classe danger de 10 le tableau ci-dessous nous donne le niveau SIL à appliquer.
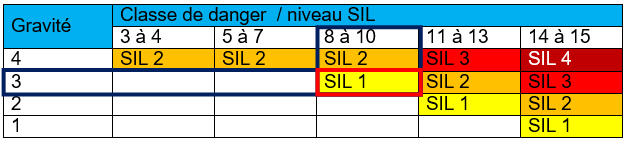
EN954-1
SIL 0 : elle n’impose aucune précaution particulière.
SIL 1 : elle impose l’utilisation de matériel de sécurité mais sans précaution particulière. Le premier défaut peut causer la perte de la fonction sécurité.
SIL 2 : elle impose l’utilisation de matériel de sécurité et doit intégrer l’autocontrôle. Vérification de la réponse de la sécurité (1=Ok ; 0=Défaut ; — =erreur).
SIL 3 : elle impose l’utilisation de matériel de sécurité et doit intégrer la redondance sur les entrées et sorties. Il faut que les deux contacts de la sécurité soient en défaut pour perdre la fonction sécurité.
SIL 4 : elle impose l’utilisation de matériel de sécurité et doit intégrer à la fois l’autocontrôle et la redondance sur les entrées et sorties. Il faut les 3 contacts en même temps d’un capteur plus l’erreur du relais de sécurité pour causer une perte de la sécurité.
Remarque : La réduction d’un risque est une contribution à la réduction globale du risque de la machine. Ainsi, il est possible d’avoir un niveau SIL requis égal à 1 sur un site à haut risque, du fait que l’ensemble des barrières de sécurité assure la réduction globale du risque suffisante. De même, il est possible d’avoir un niveau SIL requis égal à 3 sur un site à faible risque, si le reste des barrières de sécurité est quasiment inexistant.
En sécurité machine il est obligatoire d’avoir 2 contacts minimum.
Le fait d’ajouter un contact supplémentaire permet dans le cas où un contact (bouton) colle (reste enclenché) d’avoir le second contact pour assurer la sécurité. A chaque contact ajouté on divise le risque d’avoir une panne lié à un organe de sécurité.
Les relais de sécurité sont la pour apporter une protection élevée aux machines et séparer la partie sécurité du reste des commandes de la machine. Ils garantissent la protection de l’opérateur et de la machine grâce à l’arrêt immédiat.
Dans le cas d’une machine avec une grande enceinte avec de nombreux retour de sécurité (Arrêts d’Urgence, Barrières Immatérielles…) ou nécessitant un SIL2 et plus il est nécessaire d’utiliser un relais de sécurité ou un automate pour remonter l’information de sécurité sur un circuit indépendant car le risque humain est trop élevé.
Mesure de protection mise en place
Après avoir défini le risque lié à notre machine il faut appliquer un niveau de sécurité minimal au risque rencontré le plus élevé. Si dans notre étude un accident atteint un niveau de SIL2 ; l’ensemble des sécurités à appliquer seront de SIL 2 ou plus.
En cas de défaillance ou d’accident il faut pouvoir intervenir dans les plus brefs délais pour stopper la machine. Pour cela nous utilisons des relais de sécurité ou des automates de sécurité quand l’installation est plus importante comme pour une chaine de production, permettant d’avoir plus d’appareils de sécurité raccordés.
Barrières immatérielles, arrêt d’urgence, contact porte, capteur de collision, caméra de zone…
Le temps de réaction est important, si quelqu’un traverse les sécurités il faut que la machine soit arrêtée avant que la personne l’atteigne en prenant en compte le temps d’arrêt de la machine.
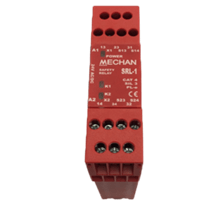
RELAIS DE SÉCURITÉ SRL1
Relais de sécurité 2 canaux redondants pour sécurité machine SIL3
-2 sorties de contact NO (normalement ouvert)
-1 sortie contact NF (normalement fermé)
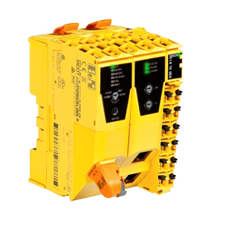
AUTOMATE DE SÉCURITÉ
SIL3 Control des modules de sécurité en temps réel, sécurité programmable, sécurité intelligente pause en cycle le temps de corriger le défaut puis reprise du cycle à la tache précédant le défaut.